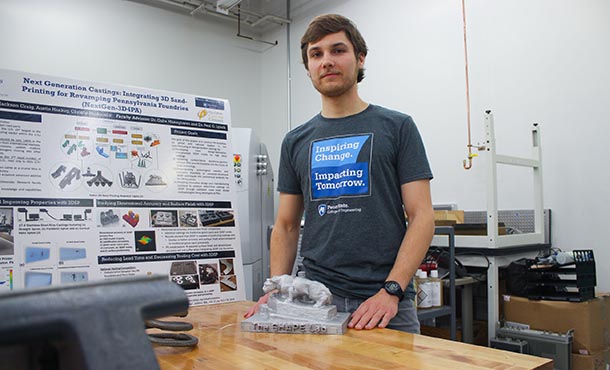
Daniel Martínez Lepp, a Fulbright scholar, will earn the first master of science degree in the additive manufacturing and design at Penn State University Park.
Fulbright Scholar earns first master's thesis in additive manufacturing and design
11/14/2019
By Erin Cassidy Hendrick
UNIVERSITY PARK, Pa. — In the fall of 2019, Daniel Martínez Lepp, a Fulbright Scholar, will earn the first master of science thesis degree in the additive manufacturing and design program (AMD) at Penn State University Park. By pioneering innovations in 3D-printed sand molds for metal castings, Martínez’s work has the potential to transform casting processes worldwide.
He was awarded the scholarship by Fulbright-Carlos Antonio López, a national graduate scholarship program in his native Paraguay, which supports 15 students to pursue STEM degrees based on their outstanding academic merit and potential to provide research solutions for wide-reaching problems across the world.
“Penn State’s additive manufacturing program really caught my attention,” Martínez said. “Coming here gave me the opportunity to work on the most cutting-edge developments in manufacturing.”
Arriving at University Park in the fall of 2018, Martínez worked alongside his adviser, Guha Manogharan, assistant professor of mechanical engineering and industrial and manufacturing engineering, in the Systems for Hybrid-Additive Process Engineering (SHAPE) Lab.
Martínez pursued two related research projects, both aimed at innovating 3D sand-printing for metal casting, which is the process of additively manufacturing custom solid sand molds for the fabrication of metal objects. The technological process of metal casting, a traditional method to forge parts that dates back 5,000 years, has been relatively stagnant for decades. Martínez and Manogharan are helping to bring the method into the 21st century.
“Casting is really the oldest manufacturing method, filling a mold with (melted) metal and popping it out like an ice cube except that the sand mold is shaken down to retrieve the casting,” Manogharan said. “Additive manufacturing is relatively the newest manufacturing method. Through this work, we are trying to bridge the fundamental knowledge gap between these manufacturing processes.”
According to the American Foundry Society (AFS), a person is never more than 10 feet away from an object created through metal casting, including support beams, automotive components and heat pumps. Although the process is ubiquitous, according to Manogharan, it is hardly perfect.
“Even under controlled conditions, it is an unpredictable process,” Manogharan said.
One reason is because in the traditional casting process, a straight-line funnel called a sprue is where the melted metal is poured into the mold. This vertical spout efficiently fills the mold’s chamber, but the journey can introduce too much velocity within the material, causing oxidation in the center of the piece, which weakens its final integrity.
“What we sought to do is control the turbulence better and reduce the velocity of the melt,” Martínez said. “If we are able to do that better, we can decrease a lot of defects and improve the mechanical performance.”
Spurring Martínez’s work was research done by Santosh Reddy Sama, another graduate student of Manogharan’s, which led them to a conical-helix shaped sprue, which resembles a strand of DNA.
“This shape minimizes the velocity and, at the same time, the length of the sprue to stop unnecessary thermal loss,” Martínez said.
Their experiments with the novel conical-helix sprue have shown a significant increase in the strength and performance of the final metal piece.
“We’re obtaining drastic increases in mechanical performance and a reduction in defects simply by redesigning the mold itself,” Martínez said. “Without any extra work, we can 3D print a sand casting that increases the quality with basically no additional cost.”
These advancements could prove integral for foundries, especially those within Pennsylvania, which boasts the second-highest number of such facilities in the nation. Demonstrating its potential impact, the work complements a Manufacturing PA Innovation grant, which pairs researchers with local manufacturers to advance manufacturing technologies statewide.
“These findings will offer a unique advantage for foundries to produce better, less defective castings,” Manogharan said.
Martínez’s second research project in the SHAPE Lab also illuminates other methods to improve the performance of 3D-printed sand-casting molds. He studied molds with different levels of binder jetting concentration, which essentially acts as the glue that bonds the primary materials together.
“We looked at how the permeability changed, how the gas flows across the mold and the impact on mechanical and thermal properties to see if we can modify the casting microstructure by changing the solidification process in the mold,” Martínez said. “Basically, we are looking at the different ways the physical properties of the mold can be changed to increase the casting quality.”
While the impact of Martínez’s work is likely to be seen within Pennsylvania’s manufacturing industry, equipped with his degree, he also set his sights closer to his home.
“Learning about all these new additive manufacturing technologies, what interested me most about it was bringing this knowledge back to Paraguay,” Martínez said. “We don’t have industrial additive manufacturing capabilities there, but there are so many opportunities for it in the future.”