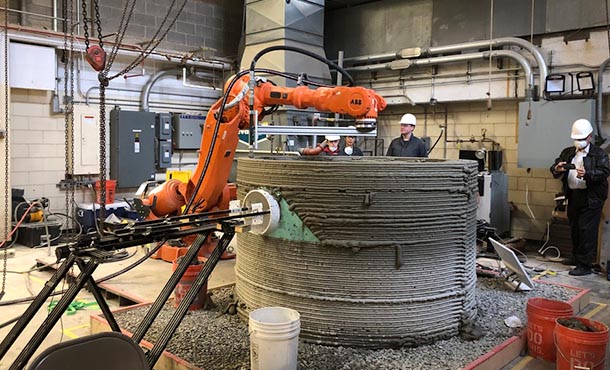
Members of the Penn State 3D-Printed Mars Habitat Challenge team test their uniquely designed dual mixer and pump 3D-printing system. The system feeds a nozzle manipulated by an industrial six-axis robotic arm to 3D print concrete. IMAGE: PENN STATE
Research team receives grant to commercialize 3D-printed concrete system
Faculty from the College of Engineering and the College of Arts and Architecture create sustainable, 3D-printable concrete structures
8/14/2019
By Samantha Chavanic
UNIVERSITY PARK, Pa. — Researchers at Penn State believe that using 3D-printing technologies to transform concrete construction processes and add new capabilities may radically transform the construction industry and reduce its carbon footprint.
An interdisciplinary team of faculty from the Departments of Architecture, Architectural Engineering, Civil and Environmental Engineering and the School of Engineering Design, Technology, and Professional Programs recently received $75,000 for its project focused on 3D-printed concrete. Funds for the project were provided by the Penn State Research Foundation, the College of Engineering’s Engineering for Innovation & Entrepreneurship (ENGINE) grant program and the College of Arts and Architecture.
Led by principal investigator (PI) Ali Memari, the Bernard and Henrietta Hankin Chair of Residential Construction and professor of architectural engineering and civil engineering, the team has built on their successful experience in NASA’s 3D-Printed Mars Habitat Challenge to commercialize its unique concrete mix and 3D-printing system. Co-PIs on the project include Sven Bilén, head of the School of Engineering Design, Technology, and Professional Programs and professor of engineering design, aerospace engineering and electrical engineering; Aleksandra Radlińska, associate professor of civil engineering; Nicholas Meisel, assistant professor of engineering design and mechanical engineering; and three faculty from the College of Arts and Architecture, including José Pinto Duarte, professor and Stuckeman Chair in Design Innovation and director of the Stuckeman Center for Design Computing; Shadi Nazarian, associate teaching professor; and Maryam Hojati, postdoctoral researcher.
Currently, conventional concrete consists of ordinary Portland cement (OPC), water, sand and aggregates. The production of each ton of OPC, the primary ingredient in concrete, requires between 1,700 and 1,800 megajoules of energy — enough to power about 500 100-watt lightbulbs for 10 hours. Production of each ton of OPC also emits about one ton of carbon dioxide into the Earth’s atmosphere. These numbers mean the cement industry generates about 5% of the total carbon dioxide emissions created by humans.
Expanding on its cement-free MarsCrete product, the researchers are designing high-performance, sustainable concrete through the development of a new cement-based mixture, primarily for home building and small building construction. Funds from the ENGINE grant are being used to complete proof-of-concept testing on the new mixture and some innovative reinforcement concepts.
The team has designed a 3D-printer system consisting of a dual mixer and pump that feeds a nozzle manipulated by an industrial six-axis robotic arm. The researchers used this system for the past two years to compete in the NASA Challenge.
“The concrete formulations and the printer system are tightly coupled, as the design of one affects the design of the other,” Bilén said. “We have to work from the micro-scale to the macro-scale. Our work is also tightly coupled to the architectural designs that can be realized via our materials and printing methods. All three — materials, printing system and architecture — must be considered together.”
Memari said once 3D-printed example buildings are created using this system, the construction industry will realize the benefits. These include minimized construction waste, faster construction, less labor, more economical construction and building in limited-resource areas or areas that are hazardous for humans.
“The technology for 3D printing of concrete is not being developed to replace conventional construction that can be carried out economically with existing methods,” Memari said. “Rather, this technology will be more useful for complex designs, where conventional methods of using formwork will be much more expensive or prohibitive.”
Through three parallel, interdisciplinary streams of research — material mixture, material characterization and design, and printing process and system — and its interdisciplinary nature, the team can better understand the effects of each variable on the printing process. According to the researchers, this will allow better control of the printing system, ultimately creating successful structures.
“The development of 3D-printing technology at the construction scale is a complex endeavor,” Duarté said. “Given the breadth and depth of the knowledge required, it would be rather difficult for a single investigator to perform meaningful research at a reasonable pace in this area. Multidisciplinary collaboration among researchers with different, complementary expertise is, therefore, essential. Penn State has a system of incentives in place that fosters multidisciplinary collaboration and the development of research like ours.”